About Us
Key Knowledge of Truck Suspension Systems: Composition, Maintenance, and Fault Handling
Views : 2
Update time : 2025-07-07 15:50:58
As a crucial component for ensuring the driving performance of trucks, the suspension system directly impacts handling, comfort, and safety. The following provides a professional analysis of its composition, maintenance essentials, and common fault handling methods.
I. Core Composition of the Suspension System
(A) Core Components
- Elastic Elements: Leaf springs are simple in structure and strong in load - bearing capacity, mostly used in the rear suspension of cargo trucks; coil springs offer excellent comfort and are commonly found in the front suspension of light - duty trucks; air springs can adjust vehicle body height and stiffness, becoming increasingly popular in high - end models; hydropneumatic springs provide precise shock absorption, suitable for heavy - duty or off - road trucks.
- Shock Absorbers: They ensure smooth driving by damping vibrations. Types include double - acting telescopic shock absorbers, gas - charged shock absorbers, and adjustable - damping shock absorbers. The latter two offer superior performance and can adjust damping as needed.
- Steering Mechanisms: Comprising control arms, thrust rods, and anti - roll bars, they respectively control wheel movement, limit axle displacement, and reduce body roll, ensuring accurate wheel trajectories.
- Connecting Components: Components such as bolts, nuts, and bushings firmly connect various assemblies to the frame and axles. Bushings effectively cushion metal - to - metal friction.
(B) System Types
Non - independent suspensions have high load - bearing capacity and low cost, suitable for heavy - duty trucks; independent suspensions offer excellent handling and are commonly used in the front suspension of light - duty and high - end trucks; balanced suspensions are applied to multi - axle trucks to evenly distribute axle loads and reduce component wear.
II. Efficient Maintenance Strategies
(A) Daily Inspections
Inspect the appearance of components before and after each trip, looking for issues such as broken leaf springs, shock absorber oil leakage, deformed steering mechanisms, and loose connecting components. Test the shock absorber damping under both unloaded and loaded conditions, and pay attention to abnormal vibrations, noises, and pulling during driving.
(B) Regular Maintenance
Replace bushings every 80,000 - 100,000 kilometers or every 2 - 3 years; replace shock absorbers when they leak oil, fail, or after 100,000 - 150,000 kilometers of driving. Promptly address issues such as broken or deformed leaf springs. Regularly lubricate moving parts, apply anti - rust treatment to vulnerable parts, calibrate front - wheel alignment parameters, and adjust air spring airbag pressure.
(C) Maintenance in Special Working Conditions
After heavy - load transportation, conduct a comprehensive inspection for leaf spring fatigue, steering mechanism deformation, and component looseness. After driving on rough roads, check for component damage, shock absorber failure, bushing wear, and clean off any attached debris.
III. Typical Faults and Solutions
(A) Abnormal Vibrations and Noises
These can be caused by shock absorber failure, leaf spring problems, loose steering mechanisms, or worn bushings. Replace failed shock absorbers, repair or replace leaf springs, tighten steering mechanisms, replace worn bushings, and lubricate components.
(B) Vehicle Body Tilting or Pulling
Differences in elastic element performance, misaligned steering mechanisms, or tire problems can lead to this. First, check the tires, then replace damaged elastic elements, calibrate the steering mechanism, and repair air spring airbag leaks.
(C) Reduced Load - Bearing Capacity
This may be due to leaf spring fatigue, insufficient air spring pressure, or component damage. Replace fatigued leaf springs, repair the air pressure control system, and strictly prohibit overloading to ensure suspension performance.
Mastering the key knowledge of truck suspension systems and implementing full - cycle maintenance strategies can significantly enhance vehicle reliability and service life, laying a solid foundation for efficient transportation.
相关新闻
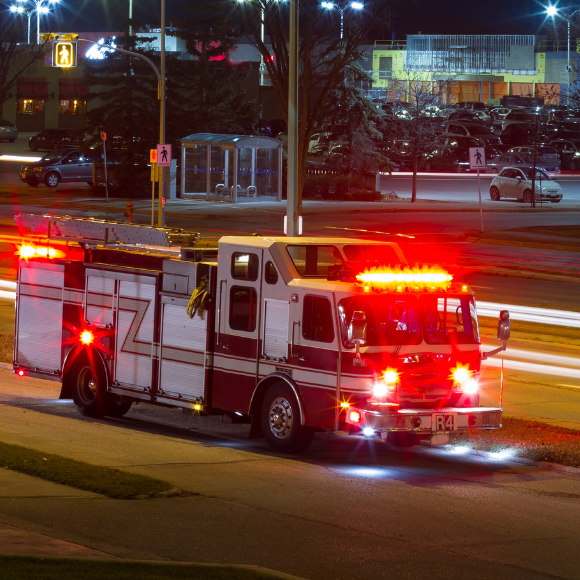
Jul 07,2025
This article analyzes truck lights, introduces the functions of lighting and signal warning lights, clarifies the replacement cycles of bulbs such as halogen, xenon, and LED, and puts forward maintenance key points under daily, regular, and special working conditions, providing guidance for ensuring driving safety and the service life of lights.
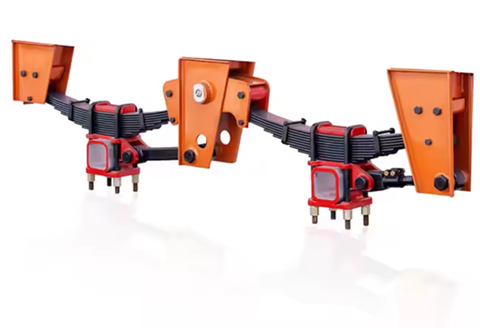
Jul 07,2025
This article analyzes the truck suspension system, which is composed of components such as elastic elements and shock absorbers. It is divided into three types: non-independent suspension, independent suspension, and balanced suspension. Maintenance includes daily inspections, regular maintenance, and handling under special working conditions. Solutions are provided for faults such as vibration and noise, body tilting, and reduced load-bearing capacity, aiming to enhance the performance and transportation efficiency of trucks.
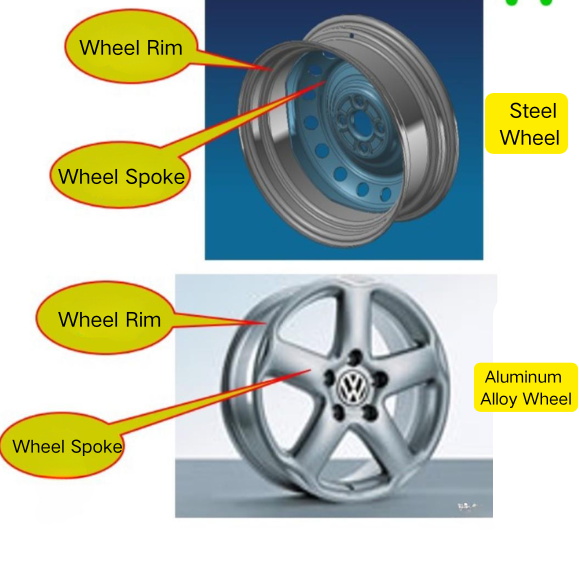
Jul 02,2025
Wheel Rim Wheel Spoke Steel Wheel
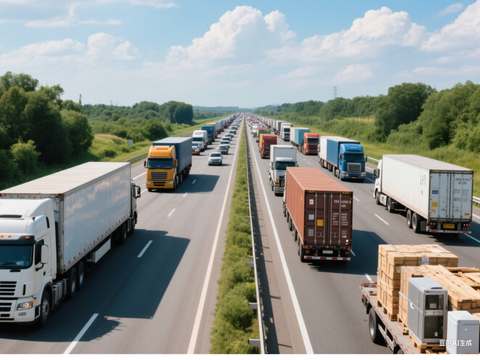
Jul 01,2025
The Birth and Development of Trucks The Birth and Development of Trucks The Modernization Process of Trucks